BANARASI SAREE
by Dr. Gautam
Chatterjee
Banarasi SAREE In the world of fashion ‘Banarasi Saree’
remains the Indian ‘SUN’ and has been a subject of great inspiration and
appreciation for world-wide costume connoisseurs. These proposed episodes
would try to fathom its historical continuance, record its traditions
which goes from generation to generation and unveil the intricacies which
goes towards making this Banarasi Saree an art and aesthetics. In short it
would enter the subject from the raw materials and show the process to the
final product and packaging.
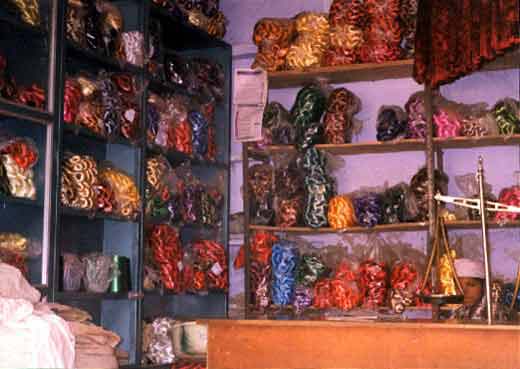
It was in the Mughal era Baranasi saree came into
popularity and got fashion currency. Today these sarees are being exported
world-wide. Around 125 km of Varanasi this art of making Banarai saree is
surviving since olden days. It was during the mughal times when all arts
be it persian, rajasthan or other indian school got amalgamated to create
a fusion of aesthetics. Same goes for costume as well. The persian motifs
and Indian designs on silk texture studded with gold and silver remained
the cue of Mughal patronage. Elaborate pure gold and silver designs are
today rare still the zari has rightfully taken its position as an apt
replacement.
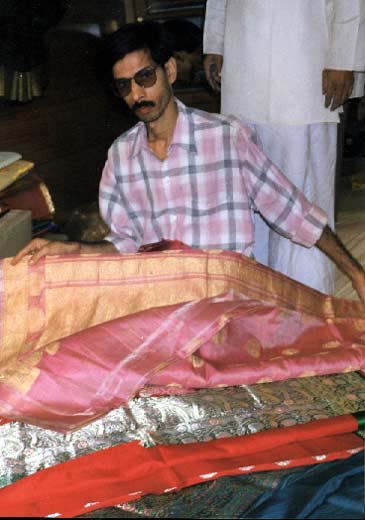
Today there are mainly four varieties of Banarasi saree
available. Those are Pure Silk (Katan); Shattir, Organza which is fine
kora with zari and silk works and finally the Georgette . If you go to
varanasi you would find some 10,000 shops selling Banarai Saree which is
more a cottage industry for several million people around Varanasi which
includes Gorakpur and Azamgarh as well. Around 60 percent of artisans are
Muslim for whom weaving this art is their tradition. Ramzan Ali,an old
traditional weaver said ‘After the partition of India people tried to take
up this art ‘Banarasi Saree’ in distant land but could not produce an
equivocal quality….there is something in this earth which makes the
creation of Varanasi Saree possible’.
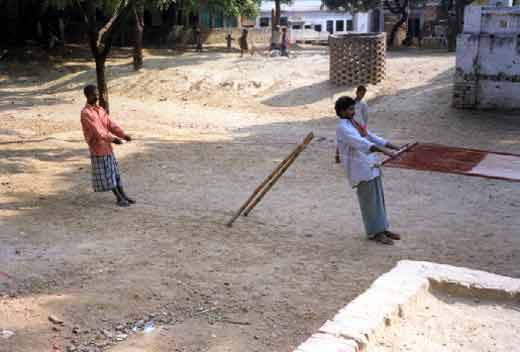
During mughal era the raw material i.e. silk used to
come from China and today those are replaced with Bangalore silks where
sericulture is an unique industry. The fineness of silk is gauged Daeonir
and quality varies from 16-18 Daning to 20-22 Daning. Still today silk
from Chinese powerloom is in great demand which comes via Nepal. Resham
cotton and zari also come from Surat which remains the cotton belt for
over several centuries.
The process of making Banarasi saree with the colourful
dying of the Silk. Those silks are then sold by weight. And powerloom
people take them to weave the basic texture of the saree. In the weaving
warp they create the base which runs into 24 to 26 mts. And there are
around 56 00 thread wires with 45 inch width. Two person tie a rope in
their waist to hold the form and other is grounded. In an elaborate
process every inch, which contains 120 silk wires, is created. Its art to
be seen only.
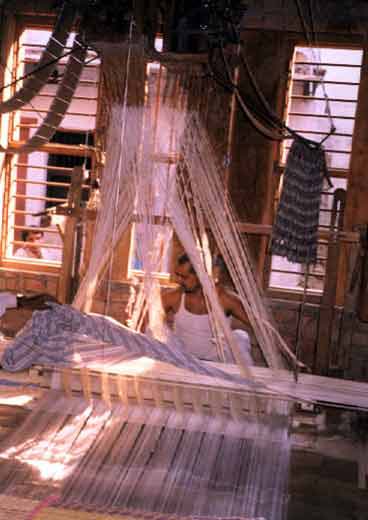
At the weaving loom three people work one weaves, one
dye and other work at the Revolving to create lacchis. At this juncture
another important process is initiated. This is designing the motifs.
There are several traditional artistis available in Varanasi who might not
be educated but can create wonder designs for Saree.
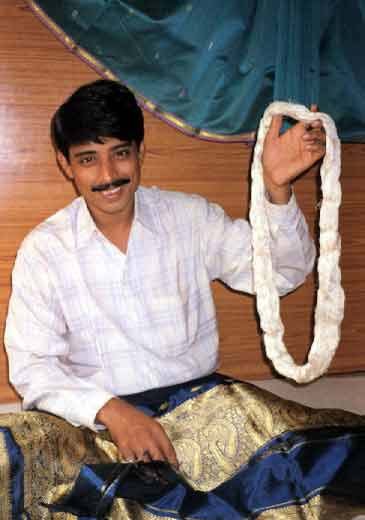
To create ‘Naksha Patta’ the artist first draw on the
graph paper with colour concepts. Now those designs are of varying kind
.But most universal kinds are Caixg(Kalka), Buti and flower and foliage.
There scene of village, fairs ,cloud ,dancing-monkey design. And even one
can see temple and mosque design. However, it was matter of experience
that in one Bride saree there were designs of ‘Grave-yard’ as well. This
became the functional aspect of art which is not far off from the people
life cycle. In modern days one can see geometrical designs have come in,
but it lacks appreciation. As traditional folk design remains the base
appeal for Banarasi Saree.
Once design is selected then small punch cards are
created those are guides for particular which colour thread has to pass
through which card at what stage. One Haquim Ali says for one small design
one requires to create hundreds of perforated cards to implement the
concept.
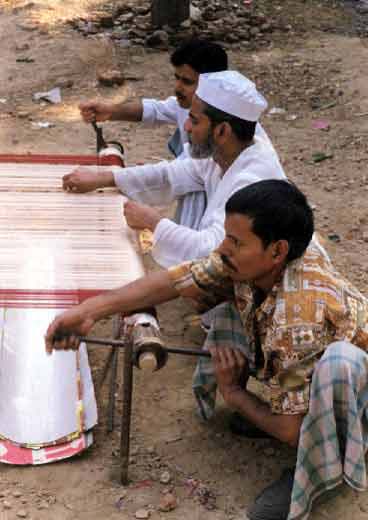
Once those perforated cards are prepared those are
knitted with different threads and colours on the loom and according to
design those are paddled in a systematic manner that the main weaving
picks up right colour and pattern to create the design and weave as well.
In yesteryears Banarasi Sarees used used to have
designs with original gold and silver thread and one manufacturer used to
take even an year to create one saree. Yet, those saress could fetch
several lakhs for the weaver. However it all depended on the intricacy of
designs and pattern A normal saree takes around 15 days to 1 month and the
time limit stretches even unto 6 months.
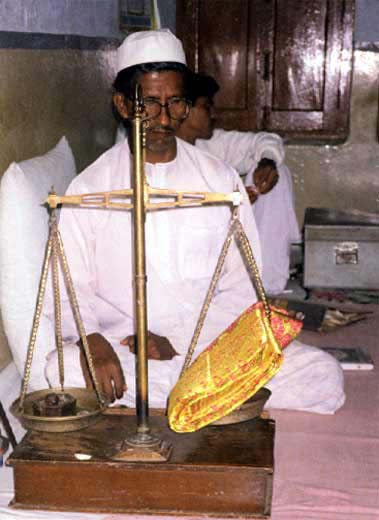
Once the saree is created those come to Gol Garj and
Kunj Gali where Banarasi sarees are sold in wholesale rates. There several
hundred shops where every morning people from different villages come to
deliver ‘created’ sarees to the market. There are some 10 shops whose turn
over they say even cross 80 crores in toto.
Thus we see for creation of Banarasi Saree one requires different experts
right from the gauging the quality of Resham until marketing. All these
goes towards creation of the unique saree which is envied by saree weavers
from all over. Its no simple weaving rather those are functional art of
India which is going on for centuries within a great fabric of Indian
traditional weavers.
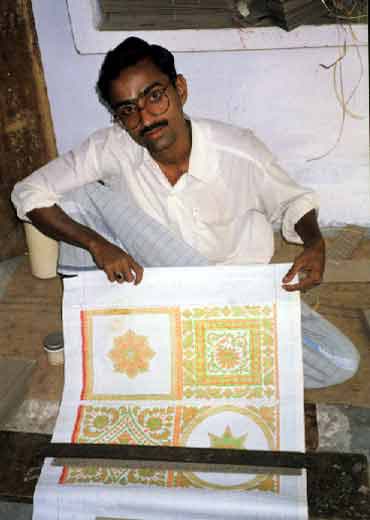